Recycling spent batteries is a critical piece of the mobility energy transition. The zero emissions future we are marching to in response to the climate crisis is only feasible with the inclusion of this key step, despite challenges. Even with the projected overcapacity for recycling batteries by 2030, keen stakeholders must be able to identify opportunities to create both environmental and financial value. The steps being taken today are critical to create this very necessary future.
As one may correctly assume, battery recycling is not the starting point for achieving the commitments to reverse human contributions to the climate crisis. It is the third in the popular reduce-reuse-recycle mantra which is still relevant:
- We must start by reducing inefficiency in transportation transitioning from oil-based energy to electricity improves efficiency by nearly 60% in some vehicles according to the Union of Concerned Scientists in a 2022 whitepaper.
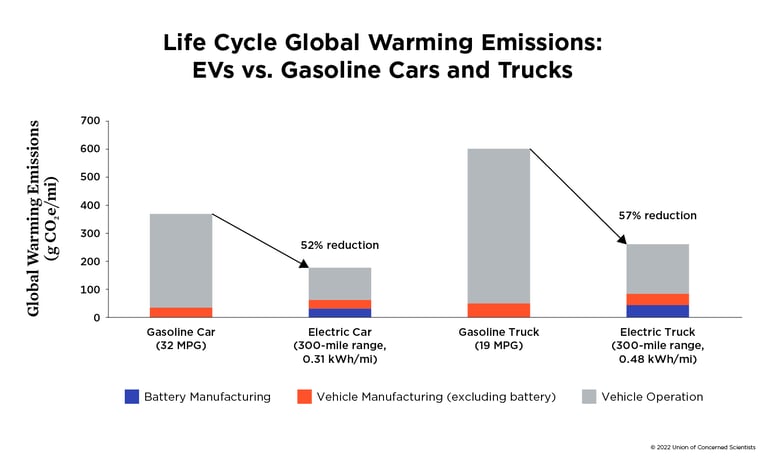
- Then, we must reuse as much as we can once we’re able to rely majorly on batteries for energy storage, making sure they are not prematurely disposed of is the next critical step. Ensuring re-manufacturing and repairs are part of the battery loop keeps us from prematurely discarding batteries leading to lost environmental & financial value. A recent whitepaper by the Automotive Recyclers Association (ARA) and ReJoule highlight some of the key opportunities like testing standards, policy support, and workforce development.
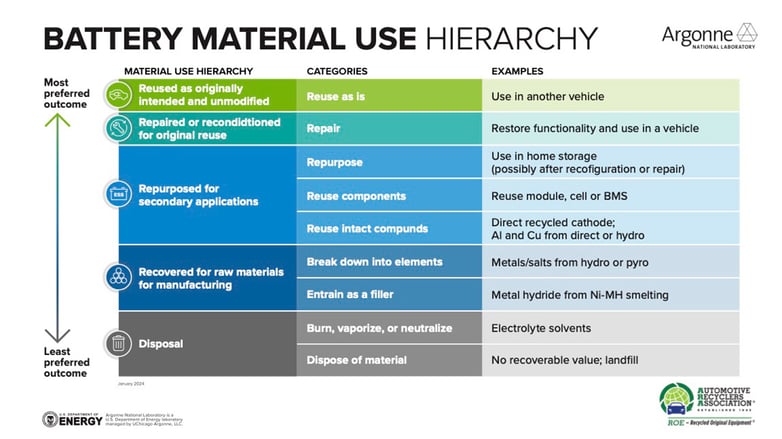
- And finally, we recycle everything that we should battery materials have a verry long shelf life, meaning they don’t get burnt up like oil. This leads to a potential for reducing CO2 emissions from batteries by up to 31% if we get it right. Recycling has long been a cornerstone of the EV promise but remains one which has a few hurdles to scale as EV adoption blossoms. We’ll spend the rest of this article unpacking this by exploring:
- Why get into recycling at all?
- Will it be worth it?
- What needs to be figured out?
- How will the leaders be differentiated?
Why get into recycling at all?
Estimated to exceed a $95 billion globally value by 2040, the path through 2030 remains uncertain. However, what is certain is that nearly all companies along the battery value chain need to understand what their relationships with recyclers will look like. Recycling companies are a lynchpin of the industry. This is because they will allow companies to have more predictability on emissions, costs, and supply.
- Starting with the source material for spent batteries, recyclers must establish relationships either directly with battery pack manufacturers (e.g., OEMs who are retaining rights to end of life batteries), cell manufacturers for their scrap, waste material collectors, or all of the above .
- On the flip side, recyclers must plug their output back into the feed source pipeline, either as precursor materials or directly producing cathodes and anodes.
Another major driver highlights regional needs with corresponding incentives to both keep energy supply local and reduce the environmental impact of making batteries by mandating local recycled content. For example,
- In China, regulations enforce EV manufacturers' responsibility for recycling end-of-life (EOL) batteries and set targets to recover 98% of nickel, cobalt, and manganese, along with 85% of lithium.
- The EU's new Batteries Regulation sets recycling targets for EOL Li-ion batteries, aiming for 65% by 2026, rising to 70% by 2031, and includes plans for using recycled materials in new batteries to create a closed-loop system.
- In the US, the Department of Energy aims for 90% recovery of lithium batteries by 2030, offering loans to recyclers, while automakers and manufacturers receive incentives for using domestically sourced or recycled materials to qualify for federal EV tax credits.
Due to the distributed network nature of the value chain, there will be a significant first mover advantage for the companies that strengthen their recycling competencies. The costs associated are estimated to be nearly $200M for an 18 kiloton facility, but there is projected overcapacity thru 2030.
Will it be worth it?
Battery recycling projections promise 13% gross margins by 2030, making them in the same ballpark as many mining companies. However, the following challenges present themselves currently:
- Ensuring availability of adequate volumes of waste batteries is critical to this promise. By 2030, roughly 20% of source material for Nickel and Cobalt are expected to come from recycling which will be most helpful if efforts progress to reduce the societal and environmental impacts of current extraction methods.
- LFP batteries which are high in lithium, iron, and phosphate are expected to reach 50% of the market by 2030. This may not be the case perpetually, but the economic viability of recycling these metals is relatively low due to the costs of virgin feedstock.
- OEMs have been known to subsidize the recycling of the less desirable materials to ensure supply and share of recycled components mandated by regulators among other reasons.
Battery recycling is essential for the energy transition in mobility, as we need to avoid replacing our dependence on oil and its emissions with a dependence on battery raw materials and their extraction impacts. However, battery recycling is not without obstacles that will cause many endeavors to fail, while few will survive and profit.
Next, we will examine the factors that determine the results and offer some guidance on what to optimize for.
What needs to be figured out?
- Relevant universal standards for battery end of life (EOL) and reuse (end of first life, EOFL) are critical due to a lack of harmonization among existing regulations, and absent guidelines. This means that some batteries with useful life remaining will be prematurely classified as EOL, limiting the true potential for emissions reduction. The industry needs to have cohesive protocols for battery end of life determination across regions, and guidelines regarding how to leverage salvaged cells for reuse need to be better established,
- Developing a sizeable workforce with the adequate skills is a pressing challenge exacerbated by the rapid growth of battery-powered applications. In a 2024 study by the Center for Automotive Research, 82% of respondents reported a shortage of “skilled local applicants”. The Battery Workforce Initiative by the US department of energy is a direct response to this challenge, looking to meet the growing demand for qualified professionals in the field.
- Reliable battery collections to ensure consistent output is critical due to the optimizations required for selected technologies and processes. These vary depending on the battery chemistries, and they are not all compatible with each other. As a result, predictability of recycled material available for sale will be challenged by the mix of battery chemistries on the market 10 to 15 years prior. Recyclers must therefore develop robust forecasting capabilities for their used battery feedstock (or black mass for purchase) to ensure they have the right supply to service their upstream demand.
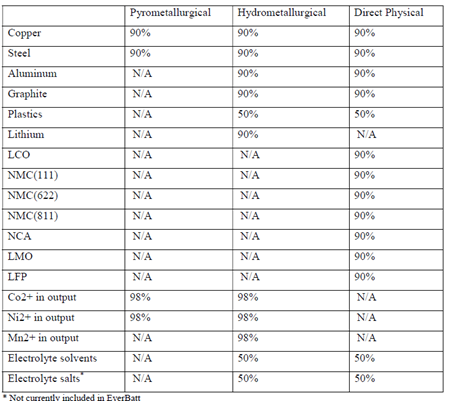
Material recovery efficiencies by technology (ANL EverBatt, 2023)
- Beneficial economics for both environmental and financial considerations at scale may take till the early 2030s to be realized. However, the foundations have been established, and the survivors will enjoy the benefits of progress achieved today. Best in class capital allocation, and operational excellence are the table stakes. Choosing the appropriate chemistries and partners will need complex planning, the right partners, incentives, and a good deal of flexibility to be responsive to the changing environment.
How will the leaders be differentiated?
- Third party evaluation of battery state of health is necessary to help the market understand the worth of a battery. Getting this right will help to validate economic models dependent on getting the most use out of batteries. Companies like Recurrent and ReJoule are taking different approaches to this opportunity. Recurrent helps EV buyers understand the residual value of the vehicles for which the battery health is a critical component. Rejoule is agnostic to battery uses but focuses on providing an independent evaluation of battery health quickly, accurately, and reliably. Being able to determine these attributes will help with the efficient movement of batteries to either reuse or recycle.
How battery state of health (SOH) maps to the battery material use hierarchy (ARA & Rejoule, 2024)- Establishing reliable systems for collecting discarded batteries will be a true differentiator for the leaders to come. It will insulate the standouts from fluctuations in quality and volume by ensuring they get the discarded stock they need. Companies like Redwood Materials have formed relationships with battery manufacturers, OEMs, electronics, and waste management companies for this purpose. Others like Cirba solutions & Ecobat have been able to establish vast networks to collect waste batteries. (Fun fact: nearly all lead-acid batteries are recycled. According to Clarios, this reduces emissions by 90% compared to using virgin raw materials).
- Lastly, operational prowess will be a key game changer even though varying strategies regarding technology, partnerships, and financing will be critical to get through to 2030. For example, Ascend Elements, Neometals, Nth-Cycle, and Li-cycle each have unique approaches.
- Nth Cycle & Ascend use more environmentally friendly processes.
- Neometals & Li-Cycle incorporate traditional hydrometallurgical acid leaching steps.
- Li-Cycle & Ascend aim to produce battery-ready active materials directly.
- Nth Cycle & Neometals focus more on producing separate metal products as output.
Across these approaches, there needs to be a disciplined consistency to produce high quality materials to meet customer needs. This more than anything else will be the most significant differentiator for leading companies.
Battery recycling is a vital but challenging opportunity that is essential for reducing emissions to address the climate crisis. The winners will need ample resources, bold market strategies, and forward-looking actions to prepare for shifts in the environment. Along with some luck. Simply being resourceful and inventive will not be enough. Patient investors are crucial. This is an excellent opportunity for oil and mining majors who want to establish a presence in the new energy economy beyond charging infrastructure.
Laolu Adeola is the Principal and Founder of Leke Services which helps the organizations driving the mobility energy transition to improve their operational performance with impacts like increased clarity and alignment, improved productivity, and reduced costs.